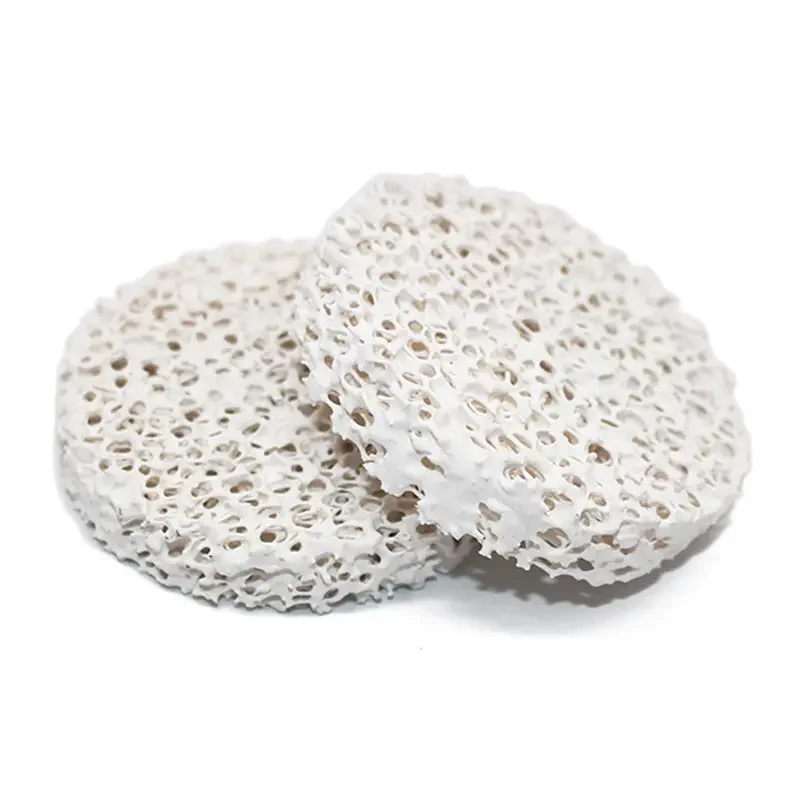
Alumina (Aluminum Oxide ) Foam Al2O3
Alumina ceramic foam insulation has excellent resistance to corrosion and corrosion of molten aluminum, so it can effectively remove inclusions. Due to its lightweight and low thermal conductivity, the foamed alumina has less accumulated heat energy and obvious energy-saving effect. The precise appearance dimensions of alumina filter bricks can speed up the masonry speed and ensure high strength and stability of the masonry.
Key Properties:
- Higher-strength than refractory ceramic fiber
- Low density
- Low thermal conductivity and linear thermal expansion coefficient.
- Great thermal shock resistance.
- Safe and rapid maintenance.
Alumina Foam Specifications
Item | SAMCFI-A1 | SAMCFI-A2 | SAMCFI-A3 | SAMCFI-A4 | SAMCFI-A5 |
Bulk density/g·cm | 0.8 | 1 | 1.2 | 1.4 | 1.6 |
Al2O3 content/% | ≥99.6 | ≥99.6 | ≥99.6 | ≥99.6 | ≥99.6 |
Impurity % | ≤0.1 | ≤0.1 | ≤0.1 | ≤0.1 | ≤0.1 |
Compressive Strength (Mpa) | ≥30 | ≥65 | ≥72 | ≥97 | ≥135 |
Reburning line change rate(1800°C×12h)% | ≤0.45 | ≤0.4 | ≤0.35 | ≤0.35 | ≤0.3 |
Heat conductivity coefficient W/(m.k) | 0.85 | 0.9 | 0.9 | 0.95 | 1.2 |
Mean temperature 1100±25°C | |||||
Working temperature/°C | 1800 | 1800 | 1800 | 1800 | 1800 |
Max. temperature/°C | 1850 | 1850 | 1850 | 1850 | 1850 |
Alumina Foam Applications
Alumina Ceramic Foam Insulation plays a crucial role across diverse industries due to its exceptional thermal insulation properties and resistance to high temperatures. In foundries and metal casting, it lines furnaces and ladles to maintain high temperatures efficiently and enhance energy efficiency during molten metal handling. It finds extensive use in high-temperature industrial processes such as kilns, furnaces, and heat treatment equipment, where it minimizes heat loss and ensures uniform temperature distribution. In aerospace and automotive applications, alumina ceramic foam insulation protects engine components from thermal stress and improves efficiency in exhaust systems. Within the energy sector, it enhances thermal insulation in boilers, turbines, and solar thermal systems, optimizing energy conversion and retention. Additionally, it serves in construction for fire protection and insulation in HVAC systems, and in electronics and semiconductor manufacturing for heat management. Alumina ceramic foam insulation’s lightweight nature, thermal stability, thermal shock resistance, and chemical corrosion resistance make it indispensable for enhancing thermal efficiency, durability, and safety in critical industrial and technological applications.
Payment & Order Questions
Most Popular Questions
Alumina foam offers superior thermal and chemical resistance, high porosity, and low weight compared to traditional materials like metals or polymers. It is also highly durable in extreme environments.
Alumina foam can withstand temperatures up to 1600°C (2912°F), making it suitable for high-temperature applications such as furnace linings and thermal barriers.
Our minimum order quantity (MOQ) varies depending on the product type. Please contact us for specific requirements.
Yes, we offer custom services, including OEM and ODM, to meet the specific needs of your applications.
Alumina foam has excellent thermal insulation properties due to its high porosity and low thermal conductivity, making it ideal for reducing heat transfer in high-temperature systems.
Yes Sure, we can provide Industrial Ceramic Samples According to Your Requirements.
Yes, many of our factories hold quality certifications, ensuring that our products meet international standards. Specific certification information can be provided based on the factory
You can contact our sales team via email or phone, or fill out the inquiry form on our website. Our technical experts are available to assist with product selection and application-specific guidance.